Die Casting Services
We offer top die casting services using 24 machines from 50 to 800 tons, with in-house mold development, machining capabilities, and the latest technology to deliver high quality products and excellent customer service.
- Products/Parts Analysis & Optimizing
- Tooling/Molds Development & Manufacturing
- Aluminum Die Casting
- Magnesium Die Casting
- Zinc Die Casting
- CNC Machining Die-casting parts
- Diverse Post processes available
Our Precision Die Casting Services
You can count on our on-demand manufacturing services to provide the most efficient and cost-effective solution at every stage of your production process.
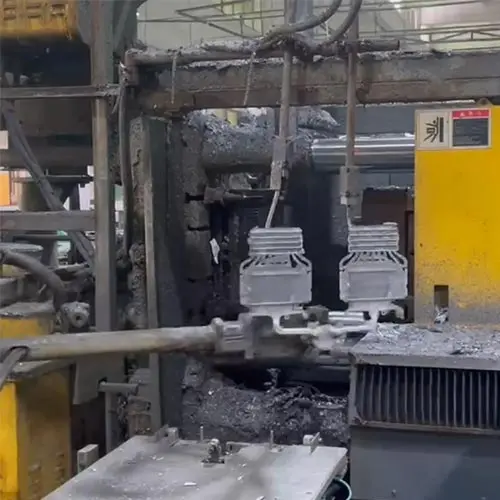
Die Casting Service
Our capabilities include manufacturing solutions for a variety of product sizes utilizing both hot and cold pressing. Our process allows for wall thicknesses as thin as 0.38mm, providing excellent dimensional accuracy and a surface finish of 0.8-3.2um Ra due to high pressures employed during the casting process.
- 24 Die-Casting Machines,50-800T
- Die-Casting Weight:From 5g to 8.6kg
- Die-Casting Material: Aluminum Alloy, Zinc Alloy,Magnesium Alloy
- Working Time: 3 shifts 24 hours
Stamping Service
Our capabilities include manufacturing solutions for parts from 0.5mm to 6.5mm thickness using progressive dies on stamping presses from 10 to 200 metric tons. Excellent dimensional accuracy down to ±0.02mm and surface finishes to 0.4um Ra are achieved through our precise tooling and processes.
- 36 Stamping Machines,10-200T
- Stamping Material: Aluminum Alloy, Stainless steel, Carbon Steel, Copper, Brass
- Working Time: 3 shifts 24 hours
In-house precision CNC machining
80% of the quality of the mold is due to the design, we strive to manufacture molds with the longest service life and fewer repairs.
- 27 CNC Machines(3-axis)
- 9 CNC Machines(4-axis)
- 3 CNC Machines(5-axis)
- 3 CNC turning-lathe Machines
- CNC Machining Material: Aluminum Alloy, Zinc Alloy,Magnesium Alloy, Stainless steel, Carbon Steel, Copper, Brass
- Working Time: 3 shifts 24 hours
surface treatment
Available Surface Finish:
- Polishing
- Sand blast
- Anodizing
- Electrophoresis
- Electroplating
- Passivation
- Powder Coating
- Painting
- Pad Painting
Our exquisite die casting capabilities
Our die-casting capabilities provide exceptional flexibility, capable of producing parts of various sizes and weights with superior accuracy and surface finish. Our commitment to adhering to ISO 8062 ST5 tolerance standards ensures high-quality products. We guarantee cost-effective solutions for clients’ projects.
Dimension | Standards |
Minimum part weight | 0.017 kg |
Maximum part weight | 12 kg |
Minimum part size | ∅ 17 mm × 4 mm |
Maximum part size | 400 mm × 300 mm |
Minimum wall thickness | 0.5 mm |
Maximum wall thickness | 12.7 mm |
Tolerance class for casting | ISO 8062 ST5 |
Minimum possible batch | 0 pcs |
Die casting Workflows
The die casting industry has many tedious flows, and die casted products are more commonly used than other material products. We provide professional manufacturing services upon quotation, to save your time and cost, so we can achieve stable production and quality from design to T1 samples testing, with fast production and accurate control on lead time.Our professional experts team is always at your service, including innovation, design, prototyping, production, testing, checks and delivery.
Mold Design
2. Mold Flow analysis
3. DFM report
4. 3D Mold drawing
Mold Making
2. Heat Treatment Report
3. Weekly Progress Report
Making samples
2. Material ROHS report
3. Limit samples&Report
MASS PRODUCTION
2. Process parameters
3. First sample test report
4. Inspection report
QUALLTY CONTROL
2. Material ROHS report
3. Salt spray test report
INSPECTION & PACKING
2. Limit samples
High pressure die casting common materials
The most commonly used materials in high pressure die casting include aluminum alloys, zinc alloys, and magnesium alloys. Aluminum alloys, such as A380 and 383, are popular for their high strength-to-weight ratio and excellent casting properties.
Aluminum die casting
Aluminum is a lightweight alloy with high dimensional stability for complex shapes and thin walls, making it castable into nearly final form. Near net shape die-casting means initial part production is close to final net shape, significantly reducing the need for precision machining and decreasing production costs by over 50%.
Lightweight
As a lightweight metal, the most popular reason for utilizing aluminum die casting is that it creates very lightweight parts without sacrificing strength.
Good Strength-to-Weight Ratio
Aluminum die cast parts also have more surface finishing options and can withstand higher operating temperatures than other non-ferrous materials.
Fully Recyclable
Since most die casting aluminum alloys are 95% post-consumer recycled material, aluminum die castings are green and sustainable.
Great Resistance to Corrosion
Aluminum die cast parts are corrosion resistant, highly conductive, have a good stiffness and strength-to-weight ratio, as well as excellent EMI and RFI shielding properties.
Excellent Electrical Conductivity
Aluminum die cast parts are corrosion resistant, highly conductive, have a good stiffness and strength-to-weight ratio, as well as excellent EMI and RFI shielding properties.
Magnesium die casting
Magnesium die castings are highly regarded for their lightweight properties, making them a popular alternative to other metal alloys. With exceptional strength and stability in more complex shapes and thinner walls, magnesium can be cast into a near-net shape, reducing the need for extensive finishing techniques after initial production.
Lightweight
Lightest of all structural metals 75% lighter than steel and 33% lighter than aluminum.
Highest Strength-to-Weight Ratio
Magnesium parts can be cast to net shape can also be used in high temperature applications.
Abundant Material Supply
Magnesium is produced from sea water, brines and magnesium-bearing minerals.
100% Recyclable
Once a magnesium die cast tool or part reaches the end of its life, it can easily be recycled to serve another purpose, saving on costs and environmental impact.
Very Good Stiffness-to-Weight Ratio
The weight of magnesium is nearly equal to many plastics and offers several distinct advantages over plastic, including superior stiffness and wear resistance.
Zinc die casting
Zinc is widely regarded as the most easily casted alloy, known for its excellent ductility, high impact strength, and ease of electroplating. Due to its low melting point and extended lifespan of die-cast parts, zinc is an economical solution for smaller components. From electronics to automotive parts, zinc die-castings are among the most widely produced products in the metalworking industry.
Good Strength and Hardness
Excellent Electrical Conductivity
Ability to Cold Form to Ease Joining
High Quality Finishing Characteristics
Outstanding Corrosion Resistance
High Thermal Conductivity
Low Cost Raw Material
Full Recyclability
High Dimensional Accuracy and Stability
Outstanding Thin Wall Capability
Available Surface Finishing Services
Surface treatment is a crucial aspect of die casting that enhances product durability, functionality and appearance. It provides metal components with protection against corrosion and wear, adds aesthetic appeal and increases product lifespan.
Painting
A coating of paint is applied to the die-cast component to improve its appearance and protect it from corrosion.
Electroplating
The process of electroplating involves the deposition of a thin layer of metal on the surface of the die cast component. The most commonly used metals for plating are nickel, chrome, zinc, and gold.
Anodizing
Anodizing is an electrolytic process that creates a protective layer of oxide on the surface of the die cast component. This improves its corrosion and wear resistance.
Powder Coating
In this process, a dry powder is applied to the die cast component and then cured using heat to create a hard, durable, and attractive finish.
Shot blasting
It is a process of cleaning or preparing the surface of the die cast component using a high-speed stream of abrasive material.
Polishing
It is the process of buffing the surface of the die cast component to produce a smooth and shiny finish.
Our Factory
Professional Manufacturer
die casting workshop
Stamping Workshop
CNC Workshop
Laser engraved surface treatment
automatic detection
Full Inspection & Packaging
Industries we serve
Automotive
Die casting is widely used in the production of automotive components, including engine blocks, cylinder heads, transmission cases, and more. The automotive industry is one of the biggest users of die casting because it can produce parts with high precision and excellent surface finish.
Industry
Die casting is also used in the aerospace industry to produce various parts, such as aircraft engine components, wing fittings, and landing gear components. Die casting enables the production of complex parts with high strength and durability that can withstand extreme environmental conditions.
Electronic
Die casting is used in the production of electronic components such as connectors, housings, and heat sinks. These components require high precision and excellent thermal conductivity, which die casting can provide.
FAQs for Die Casting
What is Die Casting?
Die casting is a manufacturing process in which molten metal is injected into a mold cavity under high pressure. The mold, or die, is made of two parts, and it has a cavity that is the same shape as the final product. When the molten metal is injected, it fills the cavity and takes on the shape of the mold. The metal is then cooled and solidified, and the finished product is ejected from the mold.
What is the process of die casting?
The die casting process includes clamping the mold, pouring, injecting, opening the mold, core pulling, ejecting, removal, spray coating, reset mechanism, and repeating the process.
- Clamping: The mold is closed, and it is ready for casting.
- Material pouring: A machine operator or robotic arm pours the molten metal into the material cylinder.
- Injection: The molten metal is injected into the mold cavity according to the process parameters.
- Mold opening: The mold is opened, and the core is pulled out using the angled guide pillar and synchronized core pulling.
- Core pulling: The mold is pushed out sideways using the core pulling device so that it can be pushed out easily. If it is front (fixed) mold core pulling, the core needs to be pulled out before opening the mold.
- Ejecting: The casting is pushed out of the mold using the ejection mechanism for easy removal.
- Removal: The casting is manually or automatically removed from the mold. If there are ejector pins, they must be removed carefully to avoid damage.
- Spray coating: The mold cavity is cleaned, and a release agent is applied before each cycle.
- Reset mechanism: If there are ejector pins below the core, a reset mechanism such as a pull rod is used to protect the mold.
- Close mold and repeat the above process.
What are the advantages and disadvantages of die casting?
Advantages:
- Precision of Dimensions: Die casting processes enable the production of parts that are uniform, dimensionally stable, and accurately meet required tolerances with higher precision compared to many other mass production methods.
- Exceptional Properties: Die-cast products boast high durability and heat resistance.
- High-Speed Production: Large quantities of identical castings can be manufactured without the need for additional post-finishing machining, resulting in efficient mass production.
- Cost-Effective: Die casting tooling equipment has a long lifespan, allowing for the production of components at competitive prices in the market.
- Complex Geometries: Die-cast products are both strong and lightweight, with the ability to achieve thin and sturdy walls that are not easily produced with other manufacturing processes. The resulting components are single parts without separate welding, fastening, or assembly, providing higher strength and stability.
- Multiple Finishing Techniques: Die casting enables products to be manufactured with various finishing techniques such as smooth or textured surfaces. This allows for plating or coating without complex preparations.
- Versatile Geometries: Die casting technologies offer the ability to produce components with various geometries such as fastening elements, bosses, tubes, holes, external threads, and more.
Disadvantages:
- Limited Compatibility with High Melting Point Metals and Alloys: Die casting may not be a suitable manufacturing process for metals and alloys with high melting points, such as steel.
- Limited Size Range: Die casting is not suitable for casting large parts.
- High Tooling Costs: The tooling required for die casting can be expensive, making it less accessible for smaller-scale production runs.
- Lengthy Delivery Time: Due to the complexity and tooling required for die casting, it can lead to longer lead times for production and delivery.
- Porosity Concerns: There is a potential for porosity in die cast products, which can trap gases during the casting process.
What are the types of die casting?
High-Pressure Die Casting: This method involves injecting the molten metal into the mold at high pressures and speeds. It is ideal for producing complex parts with tight tolerances.
Low-Pressure Die Casting: This method is similar to high-pressure die casting, but the molten metal is injected into the mold at a lower pressure. It is typically used for larger, more complex parts.
Gravity Die Casting: This is a casting process where gravity is used to fill the mold with molten metal instead of pressurized injection. It’s primarily used for casting large, heavy parts that can’t be produced through other means like low-pressure or high-pressure die casting.
Why does die casting require high pressure?
Die casting requires high pressure because it involves the injection of molten metal into a mold or die cavity under high pressure. The high pressure is needed to fill the mold completely with the molten metal and to ensure that it solidifies quickly and evenly in order to produce consistent and high-quality parts.
To fill the mold cavity: The high pressure allows the molten metal to flow quickly and uniformly into all parts of the mold cavity, ensuring that there are no voids, porosity, or other defects in the finished product.
To overcome solidification resistance: The high pressure applied also helps to overcome the natural resistance of the liquid metal to solidify, which allows the metal to flow into the smallest crevices of the mold cavity.
To prevent any air pockets or bubbles: The high pressure helps to prevent the formation of any air pockets or bubbles within the molten metal, which can cause defects in the finished product.
To speed up the process: The high pressure allows for the efficient production of high volumes of parts in a short amount of time, making die casting an economical and efficient way to produce complex and intricate shapes.
What is the maximum wall thickness for pressure casting?
The maximum wall thickness for die casting depends on several factors such as the material being used, the size and geometry of the part, and the die casting process being employed.
Aluminum: For aluminum alloys, the maximum wall thickness should not exceed 0.5 inches or 13 mm. Larger wall thicknesses can cause issues like porosity, shrinkage, and warping.
Zinc: For zinc alloys, the maximum wall thickness is around 0.25 inches or 6 mm. Wall thicknesses over this range can result in defects such as sink marks, porosity or voids.
Magnesium: For magnesium alloys, the maximum wall thickness should ideally not exceed 0.125 inches or 3 mm. Any thickness above this range can cause issues like distortion, cracking, and porosity.
Is die casting cost effective?
Yes, die casting is a cost-effective method for producing high-quality metal parts in large quantities.
High production rates: Die casting is a highly efficient process that can produce large quantities of parts quickly and consistently, minimizing manufacturing cycle times and often reducing labor costs.
Low material waste: Die casting generates very little material waste as the metal is melted and then injected into precision-crafted dies. The recycled metal can be used in subsequent casting cycles, further reducing material expenses.
High accuracy and precision: Die casting allows for precise and accurate components with tight tolerances, reducing the need for post-processing and secondary operations, which can add to costs.
Design flexibility: Die casting allows for the production of complex parts in a single operation, eliminating the need for multiple components and assembly operations, which can result in additional manufacturing savings.
Long tool life: Typically, die casting dies can last for hundreds of thousands of cycles or even millions of cycles, which makes it ideal for long-term manufacturing runs.
Repeatability: With the use of modern machinery and technology, die casting is highly automated, and hence, the repeatability of parts is high with minimal human interference.
What are the best metals to use in die casting?
Die casting is a versatile process that can be used with a wide range of metals and alloys.
Aluminum: Aluminum is a lightweight, corrosion-resistant, and versatile metal that is widely used in die casting. It is often used in the production of automotive components, consumer electronics, aerospace parts, and many other applications.
Magnesium: Magnesium is the lightest structural metal that is commonly used in die casting. It has excellent strength-to-weight ratio, is highly resistant to corrosion, and is often used in the production of automotive and electronic components.
Zinc: Zinc is a versatile and cost-effective metal that is ideal for producing small parts with intricate designs. It is often used in the production of hardware, electrical components, and automotive parts.
Copper and brass alloys: Copper and brass alloys are often used in die casting for their excellent thermal and electrical conductivity. These metals are commonly used in the production of electrical components, plumbing fixtures, and decorative hardware.
Steel: Steel is a strong and durable metal that can be used for die casting in special applications that require high strength and toughness.
Is die casting cheaper than CNC?
It depends on various factors such as the complexity of the design, material properties, production volume, and machining requirements. Generally, for small production runs, CNC (Computer Numerical Control) may be more cost-effective due to the fact that it requires less initial setup costs compared to die-casting, where it requires significantly higher costs for tooling, mold making, and other setup costs.
However, for high-volume production runs, die-casting can be a more economical choice. Die-casting allows for faster production times, lower labor costs, and is ideal for mass production of small to medium-sized components. Whereas, CNC is more suitable for producing intricate parts or highly customized parts that require precise dimensions, surface finish, and design complexity.
How long does die casting take?
The time it takes to complete a die casting project can vary based on several factors, including the size, complexity, and quantity of the parts being produced, as well as the type of material used and the finishing operations required.
Automotive Parts: The production of aluminum die-cast engine blocks for cars can take 4-6 weeks to design and create the die, with a production cycle time of 1-3 minutes per part.
Electrical Components: The production of zinc die-cast electrical components, such as connectors or housing, can take 2-6 weeks to design and create the die, with a production cycle time of 20-40 seconds per part.
Consumer Products: The production of magnesium die-cast components for consumer products, such as camera housings or laptop cases, can take 4-8 weeks to design and create the die, with a production cycle time of 20-60 seconds per part.