Mold Manufacturing
We create dependable molds for high-quality customized parts ensuring precision, fast production, competitive pricing, and reliable outputs.
- Mold follow,Mold Design, Mold Manufacturing
- Prototype Molds,low life Molds up to 1 Million-shots Molds
- Single Cavity Molds, Multi Cavity Molds,Family Molds
- Plastic Injection Molds, Die Casting Molds
Customized Tooling/Molds For Your Industries
Our services cover a wide range of fields including medical, electronics and automotive, creating top-quality injection molds for global plastics manufacturers. In addition to mold creation and design, our in-house manufacturing includes a full suite of services including OEM, injection molding,die casting & CNC
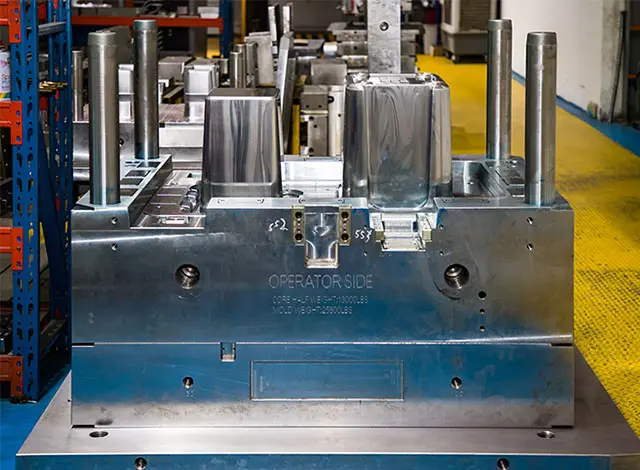
Plastic Injection Molds Manufacturing
- Precision design for high-volume production and dimensional consistency
- Ability to incorporate complex shapes and features with tight tolerances
- Injection molding tool design for manufacturability to minimize material waste and maximize efficiency
- Robust tool construction to withstand high pressure and temperature during the molding process
- Incorporation of actions, lifters, and unscrewing mechanisms to facilitate part ejection and minimize parting line flash
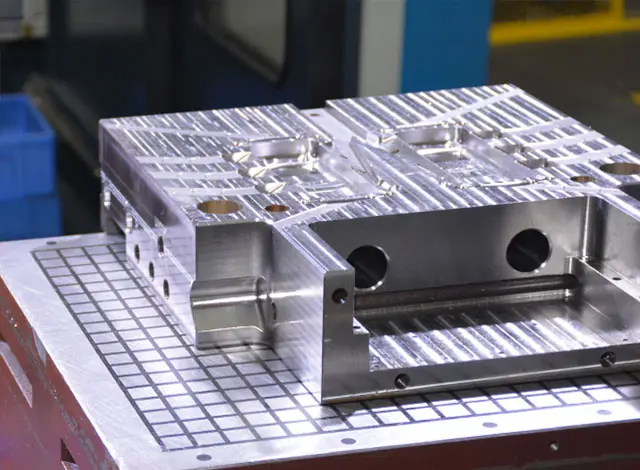
Die Casting Molds Manufacturing
- High thermal conductivity for efficient heat dissipation during casting
- Customization of gating and runner systems to optimize flow and minimize defects
- Incorporation of cooling channels to ensure consistent quality and prevent warpage or distortion
- Precision machining and tooling to ensure dimensional accuracy and repeatability
- Documented maintenance, revision, and repair services to ensure longevity and minimize downtime.
Types of Plastic Injection Molds
Perfume bottle cover Tooling/Mold
Industry: Cosmetic product packing
Mold Base steel:P20
Mold Cavity Steel :1.2083(HRC48-52)
Cavity: 8 Cavities
Mold Life:1,000,000 shot
Surface Finish:Mirror Polish
Mold Feature: Double ejection
Food Container Tooling/Mold
Industry: Foods packing
Mold Base steel:P20
Mold Cavity Steel :P20,BE-CU
Cavity: 1*1
Mold Life:1,000,000 shot
Surface Finish: Standard Polish
Mold Feature: Fast cooling for molding
Controler Housing Tooling/Mold
Industry: Electronic & Electrical
Mold Base steel: 1050
Mold Cavity Steel :1.2344(HRC48-52)
Cavity: 1*1
Mold Life:500,000 shot
Surface Finish: MT-11010
Mold Feature: YUDO hot nozzle
Electrical housing Tooling/Mold
Industry: Electronic & Electrical
Mold Base steel:S50C
Mold Cavity Steel :1.2344(HRC48-52)
Cavity: 1*1
Mold Life:500,000 shot
Surface Finish: MT-11010
Mold Feature: Colored Nylong
Medical Tooling/Mold
Industry: Medical device
Mold Base steel:S50C
Mold Cavity Steel :1.2344(HRC48-52)
Cavity: 1+1
Mold Life:500,000 shot
Surface Finish: VDI-27
Mold Feature: Family mold
Medical Tooling/Mold
Industry: Medical device
Mold Base steel:P20
Mold Cavity Steel :1.2344(HRC48-52)
Cavity: 1*4
Mold Life:1,000,000 shot
Surface Finish: Mirror Polish
Mold Feature: HASCO hot nozzle
T-branch pipe Tooling/Mold
Industry: Household
Mold Base steel:P20
Mold Cavity Steel :1.2344(HRC48-52)
Cavity: 1*1
Mold Life:500,000 shot
Surface Finish: Mirror Polish
Mold Feature: Unscrewing movement
U pipe Tooling/Mold
Industry: Household
Mold Base steel:P20
Mold Cavity Steel :1.2344(HRC48-52)
Cavity: 1*1
Mold Life:500,000 shot
Surface Finish: Mirror Polish
Mold Feature: Arc slider
Oil pipe Tooling/Mold
Industry: Automobile
Mold Base steel: S50C
Mold Cavity Steel :1.2344(HRC48-52)
Cavity: 1*2
Mold Life:500,000 shot
Surface Finish: MT-11010
Mold Feature: Multiple Sliders
Automobile Tooling/Mold
Industry: Automobile
Mold Base steel:P20
Mold Cavity Steel :1.2343(HRC48-52)
Cavity: 1*1
Mold Life:500,000 shot
Surface Finish: Mirror Polish
Mold Feature: Synventive hot nozzle
Excellent mold manufacturing capability
Much Cheaper Than Your Local Supplier
- 3-Axis, 4-Axis, 5-Axis CNC Milling
- CNC Milling Metal And Plastic
- Tolerances Of ±0.005mm
ISO 2768 CNC Machining Standard
- Facing, Taper Turning & Contour Turning
- Form Turning, Chamfering & Cutoff
- Threading, Boring, Drilling & Knurling
Approved By Over 52 Mold Makers
- Sink EDM
- Wire EDM
- Small Hole EDM
Precision Tolerances Of ±0.003 Mm
(+/-0.0001 In.)
- Centerless Grinding
- Cylindrical Grinding (OD & ID)
- Surface Grinding
Processing Flow To Get Stable Running Tooling/Molds
The person responsible for the whole steps of tool/mold manufacturing and progress tracking.
Process flow
Quotation,each order Qty. provided
Technic Documents
Product 3D drawing
Product 2D drawing with Tol.
Person in Charge
Customer
Schedule
Within 48H
Process flow
New project launches
Technic Documents
Formal product 3D drawing
Formal product 2D drawing with Tol.
Person in Charge
Customer
Schedule
When ordering
Process flow
Tooling/Mold design
Technic Documents
Mold Flow analysis if need
DFM report
3D Tooling/Mold drawing (x_t)
Person in Charge
Designer
Schedule
within 6 days
Process flow
Mold Drawing approved
Technic Documents
/
Person in Charge
Customer
Schedule
/
Process flow
Report Progress every Monday
Technic Documents
Weekly Tooling/Mold Progress Report
Person in Charge
Project Engineer
Schedule
Every Monday
Process flow
Order Tooling/Mold steel
Technic Documents
Certificate of steel,Heat Treatment Report
Person in Charge
Workshop
Schedule
/
Process flow
Mold Manufacturing
Technic Documents
/
Person in Charge
Workshop
Schedule
/
Process flow
Mold trialing and Making T1 samples
Technic Documents
/
Person in Charge
Workshop
Schedule
/
Process flow
Inspect and Send T1 samples to customer
Technic Documents
Injection parameter report
Mold Test video
Product FAI report Injection Filling balance report
Mold fitting report
Person in Charge
Project Engineer
Schedule
Day of sending sample
Process flow
Mold improvement and modification
Technic Documents
/
Person in Charge
Workshop
Schedule
Within 7 days
Process flow
Resend samples
Technic Documents
Same as T1 samples
Person in Charge
Project Engineer
Schedule
/
Process flow
Mold approved
Technic Documents
/
Person in Charge
Customer
Schedule
/
Process flow
Mold Full inspection
Technic Documents
Mould acceptance inspection report with pictures
Person in Charge
Project Engineer
Schedule
Within 3 days after Mold approved
Process flow
Mold trial production,500 shots
Technic Documents
Mold trial production pictures
Person in Charge
Workshop
Schedule
Within 3 days after Mold approved
Process flow
Rustproof packaging
Technic Documents
Rustproof packaging pictures
Person in Charge
Workshop
Schedule
Within 3 days after Mold approved
Process flow
Rustproof packaging
Technic Documents
Components & documents List for shipping
2D Mold drawing
3D Mold drawing
EDM drawing & Electrode
Certificate of steel material
Certificate of mold base
Heat Treatment Report
Mould acceptance inspection report with pictures
Person in Charge
Project Engineer
Schedule
Report filed and printed with the mold
DFM and mold design
Injection mold design begins with a DFM program (Design for Manufacturability), presenting crucial mold design information such as dimensions, cavity layout, runner system, pouring method, parting line, ejection method, mechanical design, accessories, steel selection, and cooling design. After customer approval, detailed 3D design and NC programming are carried out, taking 3-5 days for a complete design. Complex projects may require mold flow analysis or frequent part design updates, prolonging the process.
Planning, Mold base, steel and accessories preparation
Upon mold design approval, our project manager will create a detailed project schedule covering the entire process until T1 sampling. Your assigned project manager at GPMFG will provide weekly updates. Mold base and steel can be ordered immediately after design approval, while accessories like the hot runner system may have longer lead times. It is crucial to closely monitor and track these procedures to avoid delays in subsequent steps.
Rough machine
In order to obtain the desired rough shape or cavity/core, the steel must undergo initial sizing, milling, drilling, and lathe processes. Typically, a steel thickness of 0.15-0.3 mm is retained for precision machining in subsequent stages.
Heat treatment
Heat treatment is a critical process following rough machining, as it serves two key purposes: achieving specific hardness levels and attaining internal balance. For instance, materials like 1.2343 and 1.2344 typically require hardening to a range of HRC48-52.
CNC precision machining
CNC precision machining involves meticulous attention to detail. Unlike rough machining, the CNC process operates at a slower pace with reduced cutting amounts. This method produces finely machined mold inserts with a smooth, glossy finish and accurate dimensions, achieving a maximum tolerance of 0.01-0.005mm.
Wire cut and EDM
Wire cutting is specifically used for various through holes (ejector pin holes, lifters, inserts), while EDM is suitable for features that cannot be machined by CNC due to depth or narrowness. To minimize the time and cost associated with EDM, experienced designers optimize mold design by dividing the main insert into multiple sub-inserts. This allows for direct CNC machining of the inserts, reducing the reliance on wire cutting and EDM processes.
Finish and fitting
Once all the components have been completed and prepared, our engineers gather them together and expertly assemble them according to the design drawing. This crucial task heavily relies on their vast experience and exceptional skills. In some instances, certain parts may require polishing or even reworking in order to achieve a perfect fit. Moreover, the core or cavity often have specific surface finish requirements, such as texture, polish, or engraving, which are meticulously addressed.
Mold trial
When everything is prepared, we will put the mold on the injection molding machine for a test. Make sure you clearly state your requirements, how many plastic parts you need as samples, instruct the moldmaker to use the correct resin, and that injection parameters and measurement reports should be provided with the molded plastic parts.
Mold Tooling Workshops
CNC workshop
EDM workshop
Wire-cut workshop
Grinding workshop
Quality Department
Assembly Department
Selection of materials for mold making
Component Name | Steel&Hardness | Equivalent Steel | Mold Life(Shot) | Price Index | Applications |
Mold base | 1050 | 1730 | 500,000 | 1 | Plastic injection mold |
LKM P20 | 2311 | 1,000,000 | 1.35 | Plastic injection mold | |
LKM P20 | 2311 | 500,000 | 1.35 | Die-casting mold | |
H13 (HRC 44-46) | 2344(HRC44-46)/SKD61 | 1,000,000 | 2.1 | Plastic injection mold | |
Mold Cavity/Core | P20 | 2311/718H/2378 | 200,000 | 1 | Plastic injection mold |
P20H(HB330-370) | 2738H/718HH/NAK80 | 300,000 | 1.3 | Plastic injection mold | |
S136H(HB290-330) | 2083H/420H/2316H | 500,000 | 2.2 | Plastic injection mold | |
S-136 (HRC 48-52) | 2083/420ESR/2316 | 1,000,000 | 3.2 | Plastic injection mold | |
H13 (HRC 48-52) | 2344/2343/SKD61 | 1,000,000 | 3.2 | Plastic injection mold | |
H13 (HRC 48-52) | 2344/2343/SKD61 | 80-150K | 3.2 | Die-casting mold | |
8407 (HRC 50-52) | 8418 | 150-300K | 5 | Die-casting mold |
Molding analysis ensures successful mold design
GPMFG’s engineers employ finite element analysis software to simulate the behavior of molten polymers during complex injection molding processes. By analyzing the collected data, we can predict and identify potential molding issues, providing guidance to optimize designs.
1. The analysis of flow:
Predicting filling delays, hits, and balance
Analyzing mating lines, pack wind positions, and glue feeding
Determining injection pressure and closing force requirements
2. Flow channel balance analysis:
Balancing flow channel systems in multi-cavity mold cavities or families Recommending flow channel sizes and quantities for achieving flow balance
3. Gate position analysis:
Analyzing the best gate location for optimal mold flow
Automatically analyzing the position of additional gates
4. Cooling analysis:
Assessing the mold's cooling water layout
Identifying areas that require stronger cooling
Predicting molding cycle and evaluating product thickness
5. Warpage analysis:
Predicting product deformation and shrinkage values in X and Y directions
Adjusting water inlet/pressure holding parameters to reduce mold deformation
6. Shrinkage analysis:
Analyzing molding shrinkage with put number and volume
Assessing the presence of shrinkage marks
7. Gas-assisted analysis:
Predicting gas-assisted molding shrinkage and deformation
Evaluating gas penetration distance, effect, and optimal location
8. Core transfer analysis:
Predicting mold core shift trend and correcting mold design
Reducing the weak impact strength of core during filling
9. Stress analysis:
Predicting residual stress distribution and size in molded products
10. Fiber orientation analysis:
Controlling the fiber orientation of plastic, injection molded parts
Simulating percentage simulations according to different fibers
Improving material properties such as bending and tensile strength
11. Overmolding analysis:
Analyzing flow, warpage, and bonding in two-color molding
12. Microchip encapsulation analysis:
Predicting chip encapsulation, flow, and curing conditions in mold cavity
Assessing the effect of flow on gold wires and pins
13. Bottom fill analysis:
Optimizing thermoset molding conditions and fill dispensing model simulation
Predicting various forms and injection pressure/clamping force requirements
14. Birefringence prediction:
Adjusting gate position, process conditions, or modifying product structure to achieve low residual stress
Predicting the occurrence and severity of asymmetric birefringence in optical parts.
FAQs for Mold Manufacturing
What information should be provided to obtain the quotation?
Formal product 3D drawing
Formal product 2D drawing with Tolerance
Parts mateirla
Molds Cavity number if exporting molds
Injection point type if exporting molds
Molds cavity steel if exporting molds
Molds frame steel if exporting molds
Molds life if exporting molds,shot
What’s the process for injection mold making?
In order to meet the requirements of customers, GP MFG designs molds and manufacturing processes through analysis and strict molding process, to ensure the perfect increase in the production of molds.
Step 1: Provide DFM report and mold flow analysis report for customer confirmation
Step 2: Provide design mold drawings for customer confirmation
Step 3: Provide reconfirmation of the drawing after modification of the mold design
Step 4: After the drawing is confirmed Ok, start to arrange the mold manufacturing
Step 5: Provide weekly tooling progress report
Step 6: Send out T1 sample until the mold is confirmed Ok
Can you customize the mold according to my sample?
Yes.
- If accurate product drawing is available,attach 2D product drawing with tolerance and 3D product drawing.
- If you have accurate sample, if there are no drawings or only sketches, please provide the final sample,we will arrange to make a DFM report to send to you for confirmation, and then design the mold.
How much does a mold cost?
The cost of the mold is affected by the size and material of the product,the complexity of the structure and the quantity of production,and the surface requirements, and so on.Because of the great difference,the price of the mold can not be estimated.If you want to know the cost of mold precision,please send email to us.
How long does it take to make a mold?
It depends on the complexity of the product structure,the specific delivery time will be indicated on the quotation sheet.The following delivery dates are for reference:
20-30 days for molds less than 1 ton
30-45 days for molds from 1 ton to 3 tons
45-60 days for molds from 3 ton to 5tons
How long is the mold life? How to protect?
In the mold industry,the life grade of the mold is divided into:100 thousand times,300 thousand times,500 thousand times and 1 million times.The die life is related to the die steel,which is selected according to the plastic material,the surface treatment of the parts and the potential production quantity.
Mold exported to customers in your country or region,in the correct use of die mold and regular maintenance,the service life of the actual can completely meet the design service life,a failure if the life of the mold in a reasonable period,our project engineer will evaluate the replacement parts or mold repair solution,will arrange manufacture and send again.